Raise Your Jobs with Aluminum Casting Illinois: Let's Collaborate
Raise Your Jobs with Aluminum Casting Illinois: Let's Collaborate
Blog Article
Mastering the Craft: Professional Tips for Flawless Light Weight Aluminum Spreading Results
In the realm of aluminum spreading, accuracy and knowledge are critical to attain remarkable results. Grasping the craft requires a careful understanding of the devices and equipment at one's disposal, an eager eye for preparing the light weight aluminum alloy to specific specifications, and a nimble hand in utilizing optimal casting techniques.
Essential Devices and Tools
Aluminum casting needs details devices and tools to guarantee precision and performance at the same time. Critical tools include a crucible, ladle, furnace, and mold and mildew. The crucible, typically made from graphite or ceramic materials, withstands heats needed to melt aluminum. A well-insulated heating system qualified of getting to temperatures over 1200 ° C is vital to liquefy the steel. The mold and mildew, usually constructed from steel or sand, shapes the liquified light weight aluminum right into the preferred form. A ladle is used to transfer the liquid steel from the crucible to the mold and mildew without spillage.
Furthermore, tools like gloves, aprons, and tongs are needed to make sure the security of drivers working with molten aluminum. Spending in high-grade devices and tools not just enhances the accuracy of light weight aluminum casting however additionally adds to a much more reliable and secure production process.
Preparing the Light Weight Aluminum Alloy
To ensure the success of the aluminum spreading procedure, meticulous prep work of the alloy is critical. The initial step in preparing the light weight aluminum alloy is to very carefully select the suitable kind of aluminum based on the attributes required for the final item. Elements such as toughness, rust resistance, and machinability require to be considered when picking the alloy. Once the alloy kind is identified, it is necessary to effectively clean the light weight aluminum to eliminate any type of contaminations that can influence the casting high quality. This can be done via methods like fluxing, degassing, and filtering.
After cleaning, the next vital step is to heat the aluminum to the proper temperature level for casting. This procedure, called alloy melting, makes certain that the light weight aluminum remains in its molten form and all set for casting (aluminum casting illinois). Furthermore, managing the temperature level during melting is crucial to stop overheating or underheating, which can result in issues in the final product. Generally, careful preparation of the light weight aluminum alloy establishes the foundation for a successful casting process and high-grade end results.
Ideal Casting Strategies
Implementing specific casting techniques is essential for achieving top notch outcomes in aluminum spreading procedures. The aluminum should be heated to the ideal temperature level to minimize issues like contraction and porosity in the final cast.
Furthermore, preserving constant pouring rate and pressure is vital to attaining harmony in the actors piece. Stable and slow putting helps stop turbulence and air entrapment, which can lead to blemishes. An additional crucial aspect is the use of degassing representatives to remove impurities and gases from the liquified aluminum, resulting in a cleaner final product.
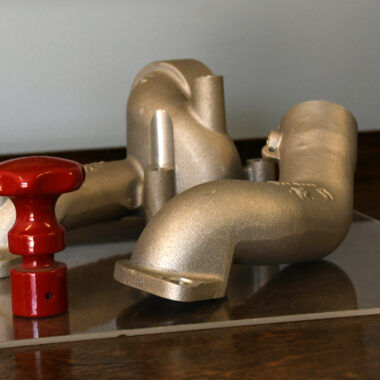
Getting Smooth Surface Area Ends Up
For producers seeking to improve the visual charm and quality of their aluminum castings, achieving smooth surface area finishes is an important facet following accurate spreading strategies and correct cooling procedures. One key approach to attain smooth surface coatings is by using high-quality molds that are appropriately prepared and preserved. The mold surface area ought to be meticulously cleaned up and covered with launch representatives to avoid imperfections transferring onto the actors aluminum during the cooling procedure.
Moreover, controlling the cooling price of the light weight aluminum casting is crucial for achieving a smooth surface coating. Rapid air conditioning can lead to thermal gradients that bring about surface flaws, while slow cooling might trigger microstructural issues - aluminum casting illinois. By applying controlled cooling procedures, such as using air or water quenching techniques, manufacturers can guarantee that the light weight pop over to this web-site aluminum strengthens evenly, reducing the chance of surface flaws
Along with mold and mildew high quality and cooling procedures, post-casting therapies like shot blasting or chemical etching can further refine the surface area finish of aluminum spreadings. These strategies help smooth out any kind of remaining roughness or pollutants, resulting in a flawless appearance that satisfies the highest high quality requirements.
High Quality Control and Troubleshooting
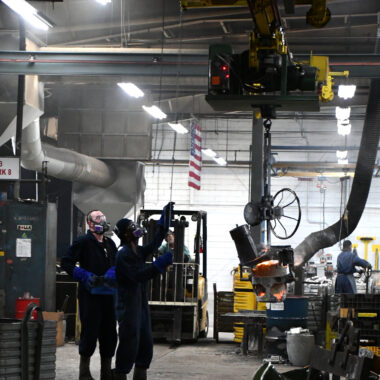
In the world of troubleshooting, it is vital to have a detailed understanding of usual flaws that see post can occur during aluminum casting, such as surface, shrinkage, or porosity abnormalities. By conducting origin evaluation and carrying out rehabilitative procedures, suppliers can avoid these issues from recurring in future spreading runs. Efficient troubleshooting not just boosts the general quality of cast aluminum items however additionally improves process efficiency and minimizes production prices. Continuous enhancement with quality assurance and fixing practices is fundamental to accomplishing flawless lead to light weight aluminum spreading.
Verdict
Finally, grasping the craft of light weight aluminum casting calls for necessary devices and equipment, appropriate preparation of the light weight aluminum alloy, optimal casting strategies, attaining smooth surface area coatings, and executing quality assurance procedures. By following these expert ideas, flawless outcomes can be accomplished in light weight aluminum spreading processes. Quality assurance and troubleshooting are essential aspects to take into consideration to guarantee consistent and high-grade cause aluminum spreading jobs.
The initial action in preparing the why not find out more light weight aluminum alloy is to thoroughly choose the appropriate type of light weight aluminum based on the attributes needed for the final product.Executing exact spreading methods is important for attaining top quality results in aluminum spreading processes. By understanding these ideal casting methods, manufacturers can regularly produce perfect light weight aluminum castings.
For suppliers looking for to boost the aesthetic allure and quality of their aluminum castings, achieving smooth surface area finishes is a crucial aspect following accurate casting techniques and correct air conditioning treatments.In conclusion, understanding the craft of aluminum casting requires crucial devices and devices, correct preparation of the aluminum alloy, optimum casting strategies, accomplishing smooth surface area coatings, and carrying out quality control procedures.
Report this page